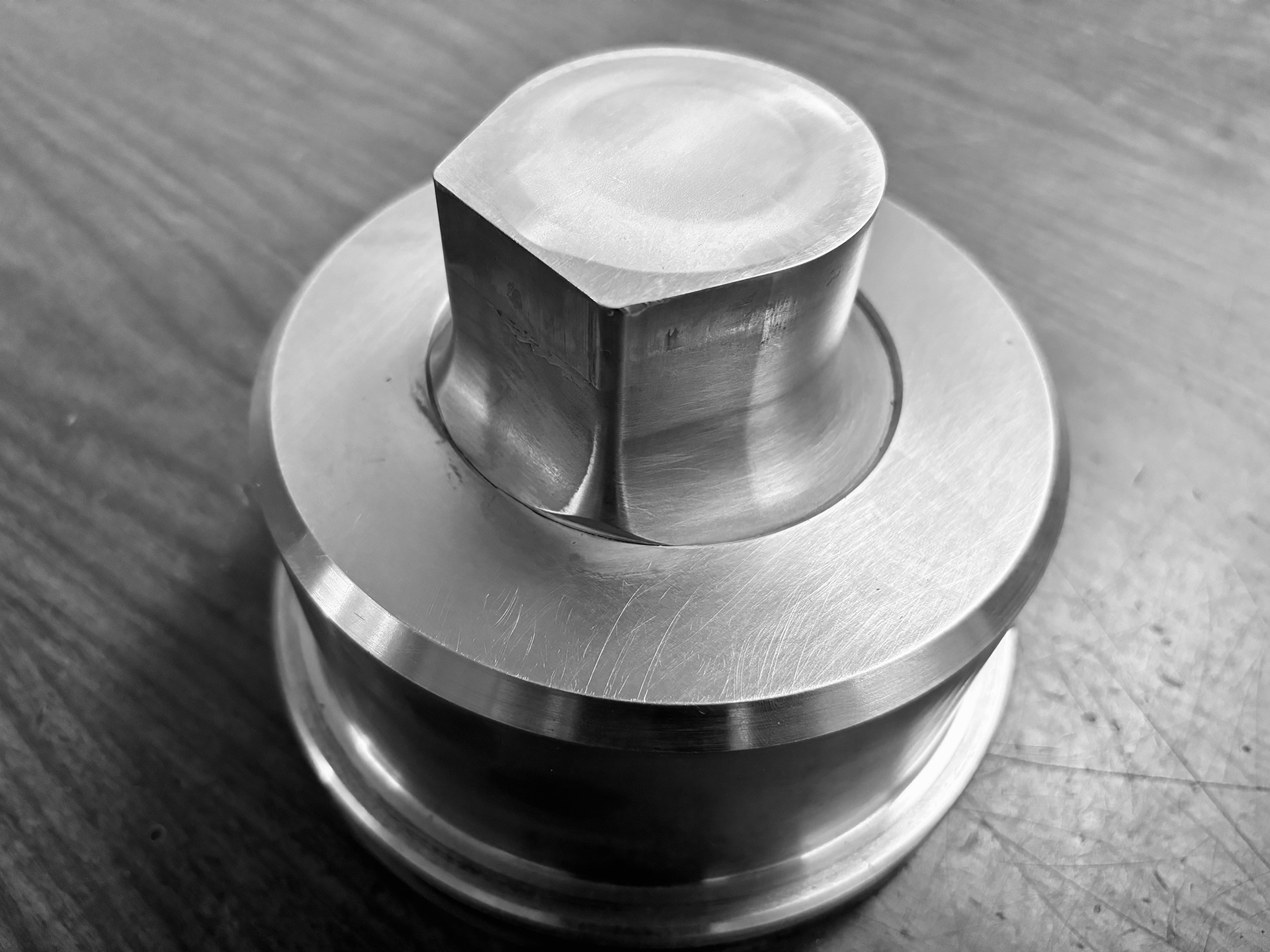
COLD FORGING
Our company specializes in cold forging technology, which utilizes press machines to smoothly shape materials into three-dimensional products. Cold forging reduces reliance on cutting and machining processes, resulting in high-quality finished products with minimal material usage and reduced environmental impact. The shortened production time also leads to significant cost savings.
Cold forging enables the production of complex shapes that are difficult to achieve with traditional cutting methods, resulting in products with reduced mechanical stress and uniform hardness. Furthermore, compared to other manufacturing processes, cold forging ensures high strength and resistance to abrasion.
There are two primary methods of forging: free forging, which uses a hammer, and die forging, which uses dies. Additionally, forging can be classified based on the temperature at which it is performed: cold forging (at room temperature), warm forging (600-900°C), and hot forging (900-1250°C).
We adopted forging technology at an early stage, enabling us to supply high-precision products for automotive and speaker components. These products are distinguished by their excellent quality, cost-efficiency, and environmental friendliness.
Continuing our commitment to innovation, we have advanced to using cold forging to enhance the value of our products.
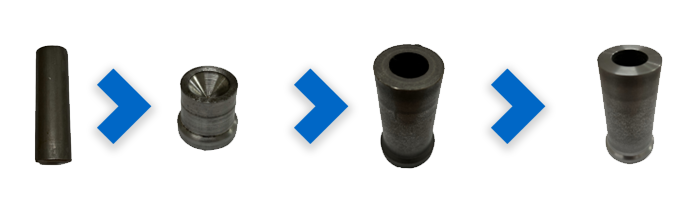