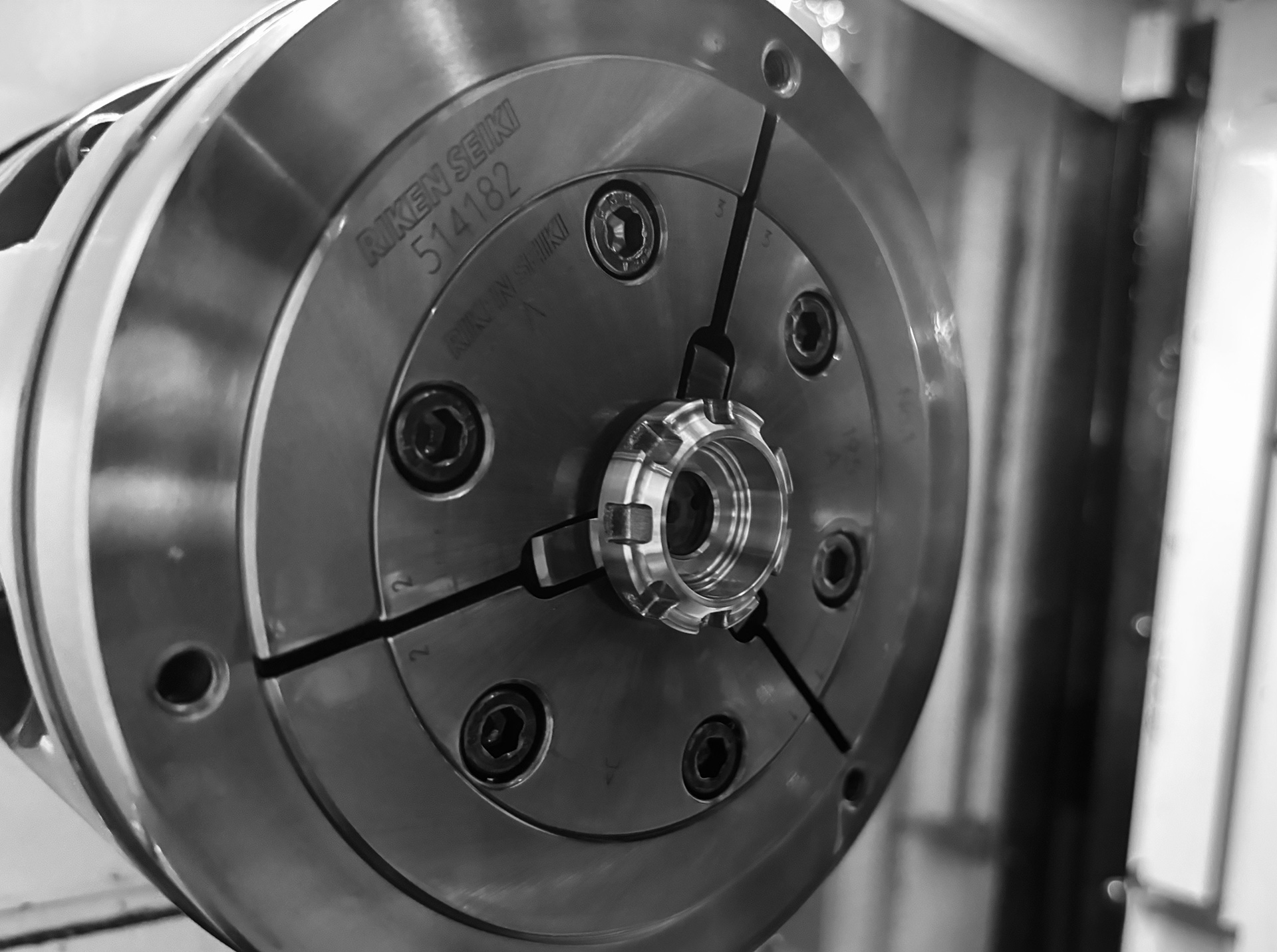
SINCE OUR FOUNDATION IN 1951
We have developed extensive expertise in handling a diverse range of products, from speaker components to automotive parts, consistently pushing the boundaries of innovation.
We excel in selecting the appropriate material type, such as coils or bars, based on product specifications. At the customer’s request, we can propose suitable designs and execute integrated manufacturing, from raw coil material to the finished machined product.
For more details on each process, please click on an icon from PARTS FORMER to MACHINING.
RAW MATERIAL
Our raw materials consist of steel coils of various types, selected according to customer specifications. We have extensive experience working with the following steel grades:
– SAE-series
– SCr-series
– S-series-C
– SWRCH-series
– ELCH2
We are capable of processing steel coils with diameters ranging from Ø11.35 to Ø38 millimeters.
PART FORMER
Parts Former is a “transverse automatic press machine.” These machines work with coiled material, straightening it, cutting it to a specific volume, and molding it several times as it is conveyed.
Our machines can mold the material through a maximum of four stages within a single machine. In other words, we can achieve molding for five processes, including cutting, with one machine.
The primary advantage of the Parts Former is its ability to drastically reduce lead time and in-process inventory by simultaneously cutting and molding the material.
Main Facility | |||
PF538LH | |||
Max. diam. for cutting off: | ø38mm | ||
Max. capability for cold forging: | 6000 KN | ||
Max. length for cutting off: | 230mm | ||
Cutting off Capability: | 500N/mm2 | ||
Equipment List | Steps | Quantity | Brand |
PF538LH | 5 steps | 1 | JINU FT CO.,LTD |
APF380 | 3 steps | 1 | Asahi Sunac Corporation |
OBF320 | 2 steps | 1 | Asahi Sunac Corporation |
OBF200 | 3 steps | 1 | Asahi Sunac Corporation |
ANNEALING
In this process, a metal blank is heated to reduce the hardness generated during the previous forming operation and to increase its ductility for the subsequent pressing process. Annealing is essential to reduce the load on dies and molds during the pressing operation.
Equipment List | Qty | Capacity | Brand |
Non-Oxidation furnace | 1 | 5T | Hosoda |
Speria annealing furnace (pit type). | 2 | 3T | Oriental |
Electric furnace (pit type). | 1 | 2.4T | Denkiro |
SHOT BLAST
Shot blasting is a process used to clean the metal surfaces. This technique involves forcibly propelling a stream of abrasive material, called “shot ball,” against the surface of the metal under high pressure. The shot material is composed of steel, and the size and type of the shot can vary depending on the application.
This process removes rust, scale, and other contaminants from metal surfaces to prepare them for further processing, such as painting, coating, or welding.
Shot blasting is a surface treatment method used to remove the oxide film, or scale, generated on the surface of a metal blank during the annealing process.
This is achieved by projecting small steel balls onto the surface.
The primary objectives of this process include:
- Removing the oxide film formed during the annealing process.
- Preparing the surface for lubrication (e.g., bonderizing).
- Preparing the surface for plating.
- Removing burrs and imperfections.
Equipment List | Qty | Capacity | Brand |
NTF-100LAP | 1 | 500 Kg | Nicchu CO.LTD |
NTSF-200LAP | 1 | 1000Kg | Nicchu CO.LTD |
BONDERIZING
Bonderizing (phosphating) is a surface treatment applied to coat a blank with a lubricant film prior to the press process. This lubricant film reduces friction between the blank and the dies during pressing, preventing burn marks and facilitating smoother press forming.
Additionally, it extends the life of the dies. Moreover, this treatment is effective in preventing rust on the blank.
BONDERIZING FLOW CHART
Equipment List | Qty | Capacity | Brand |
JBM-1 | 1 | 6 Barriles | JYOTO W |

PRESS
Our press process can transform unfinished materials into ideal shapes using various processing methods. This process plays a crucial role in our company’s forming operations.
One of our press machines can exert up to 650 tons of pressure, the highest among the machines we own. Currently, we have a total of 11 press machines, with pressure capacities ranging from 60 to 650 tons. This range allows us to select the most suitable machine for a wide variety of processing conditions.
This flexibility is the greatest advantage of our press process.
Main Facilities | ||
LIC630 | ||
Capacity | 630T | |
Slide stroke | 180mm | |
Die height | 520mm | |
Slide adjustment | 50mm | |
KP-650 | ||
Capacity | 650T | |
Slide stroke | 160mm | |
Die height | 400mm | |
Slide adjustment | 15mm | |
List | Quantity | Brand |
LIC630 | 1 | Komatsu Industries |
KP-650 | 2 | Chin fong industrial. |
KP400 | 1 | Chin fong industrial. |
LIC400 | 1 | Komatsu Industries |
KP250 | 1 | Chin fong industrial. |
LIC250 | 1 | Chin fong industrial. |
OBS150 | 2 | Komatsu Industries |
OBS80 | 1 | Komatsu Industries |
OBS60 | 1 | Komatsu Industries |
MACHINING
Our machining process is integral to finishing products from molded materials with high precision. During this process, we finish the surfaces of pressed or trimmed materials to meet the exacting dimensions specified by our customers. This includes creating holes and tapping screws, tasks that are often challenging in the forging process.
We operate a state-of-the-art facility equipped CNC lathes with a single spindle, and composite lathes with dual spindles. The NC lathes are ideal for one-sided material processing, delivering consistent and precise results. For more complex shapes or double-sided processing, our composite lathes provide the flexibility and capability needed to handle these intricate tasks.
The dual-spindle composite lathes can process two materials simultaneously during one-sided operations, significantly enhancing our productivity and efficiency. By selecting the appropriate machine based on the specific processing requirements, we can optimize our operations, improve productivity, and reduce costs.
Our commitment to utilizing the most suitable machinery for each task ensures that we consistently deliver high-quality, precision-finished products to our customers.
Machining | ||
List | Quantity | Brand |
CNC lathe (X100) | 6 | Takamaz |
CNC lathe (XC100) | 9 | Takamaz |
CNC lathe (GSL10) | 1 | Takamaz |
CNC lathe (LB300) | 2 | Okuma |
CNC lathe (USL-480) | 1 | Takamaz |
2 spindles CNC lathe (XW-30) | 4 | Takamaz |
2 spindles CNC lathe (MW100) | 3 | Muratec |
2 spindles CNC lathe (MW40) | 1 | Muratec |
CNC (Chamfering) | 1 | Sanyo |
CNC (Broaching) | 1 | Nachi |
Centerless grinding | 1 | OHMIYO |